Contributing Editor: Dave Davidson: | dryfinish@gmail.com | 509.563.989
https://dryfinish.wixsite.com/iso-finish | https://dryfinish.wordpress.com
Free Sample Processing | Contract Finishing | Equipment and Tech Assistance
Above: Bobby Whiteman, MacKay’s Centrifugal Isotropic Finishing Systems technician explains the improvements with edge and surface finish now realized from utilizing CIF processing to Debbie Holton from the Society of Manufacturing Engineers. Bobby and Katie MacKay, (The Executive VP) are explaining that MacKay has been receiving

customer feedback on the improved part uniformity and quality now achieved with CIF processing. This is a substantial improvement over parts processed with the hand-deburring previously performed. See also Katie narrating an SME produced video on their use of Centrifugal Isotropic Finishing on their precision parts.
MacKay Manufacturing is a contract manufacturer located in Spokane, WA. that has a 50,000 square foot facility and close to 140 employees, the company machines and manufactures parts for the aerospace/defense, medical/surgical, electron microscope and a host of other industries. The company is also a recipient of the Washington State Manufacturer of the Year Award. See more information in the recent newspaper article: http://www.spokesman.com/stories/2017/jul/17/doug-clark-mackay-manufacturing-a-well-kept-spokan/
The SME presentation below outlines how MacKay Manufacturing adopted high-speed centrifugal isotropic processing to upgrade their deburring and finishing procedures a part of their lean implementation program. The company previously utilized both vibratory finishing and considerable hand-deburring. Almost all part finishing is now performed with centrifugal processing. Hand-deburring procedures have been minimized significantly or eliminated, Edge and surface finish quality has improved as the equipment with four separate processing compartments easily accommodates the running of several different part processes simultaneously. Abrasive deburring and smoothing processes can be followed up with dry process polishing processes which can produce low micro-inch Ra surface values of exceptional quality. See the operating videos that are shown below to see how high-energy finishing can produce highly polished surfaces. In the second video, Katie MacKay, MacKay’s Executive Vice-President will show how they use this process to develop highly finished and polished surfaces on coffee/espresso machines for Starbucks.
_____________________________________________________________
Mass Finishing technology for deburring, finishing and polishing of machined and manufactured parts and components
Centrifugal isotropic Finishing
Centrifugal Isotropic Finishing (CIF) is a high-energy finishing method, which has come into widespread acceptance in the last few years. Although not nearly as universal in application as vibratory finishing, a long list of important CBF applications have been developed in the last few decades.
Similar in some respects to barrel finishing, in that a drum-type container is partially filled with media and set in motion to create a sliding action of the contents, CBF is different from other finishing methods in some significant ways. Among these are the high pressures developed in terms of media contact with parts, the unique sliding action induced by rotational and centrifugal forces, and accelerated abrading or finishing action. As is true with other high energy processes, because time cycles are much abbreviated, surface finishes can be developed in minutes, which might tie up conventional equipment for many hours.
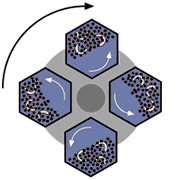
(DIAGRAM: Left) Centrifugal Barrel Finishing principles – high-intensity finishing is performed with barrels mounted on the periphery of a turret. The turret rotates providing the bulk of the centrifugal action, the barrels counter-rotate to provide the sliding abrasive action on parts.
The principle behind CBF is relatively straightforward. Opposing barrels or drums are positioned circumferentially on a turret. (Most systems have either two or four barrels mounted on the turret; some manufacturers favor a vertical and others a horizontal orientation for the turret.) As the turret rotates at high speed, the barrels are counter-rotated, creating very high G-forces or pressures, as well as considerable media sliding action within the drums. Pressures as high as 50 Gs have been claimed for some equipment. The more standard equipment types range in size from 1 ft3 (30 L) to 10 ft3, although much larger equipment has been built for some applications.
Media used in these types of processes tend to be a great deal smaller than the common sizes chosen for the barrel and vibratory processes. The smaller media, in such a high-pressure environment, are capable of performing much more work than would be the case in lower energy equipment. They also enhance access to all areas of the part and contribute to the ability of the equipment to develop very fine finishes. In addition to the ability to produce meaningful surface finish effects rapidly, and to produce fine finishes, CBF has the ability to impart compressive stress into critical parts that require extended metal fatigue resistance. Small and more delicate parts can also be processed with confidence, as the unique sliding action of the process seems to hold parts in position relative to each other, and there is generally little difficulty experienced with part impingement. Dry process media can be used in certain types of equipment and is useful for light deburring, polishing, and producing very refined isotropic super-finishes.
Below are some process video footage demonstrations of high-speed centrifugal isotropic finishing. These automated edge and surface finishing methods are capable of producing very refined low micro-inch surfaces that can improve functional part performance and service life.
Contributing Editor: Dave Davidson, Deburring/Finishing Technologist 509.230.6821 | dryfinish@gmail.com | https://about.me/dave.davidson
If you have parts that need edge or surface finishing improvement and would like to have FREE sample part processing contact Dave Davidson at dryfinish@gmail.com I can also be reached at 509.563.9859. Before we start a sample processing project I have some questions for you. Can you complete this “Request for Sample Finishing” form? This will help us to better understand your part finishing needs and assist our process engineering and equipment recommendation efforts.
SEE: https://drive.google.com/open?id=1wPg-CeP4KWHjreLBsSjb1JsR2KC2zG0oOaISqmxShaU
CONTRIBUTING EDITOR BIOGRAPHY – David A. Davidson, [dryfinish@gmail.com]
Mr. Davidson is a deburring/surface finishing specialist and consultant. He has contributed technical articles to Metal Finishing and other technical and trade publications and is the author of the Mass Finishing section in the current Metal Finishing Guidebook and Directory. He has also written and lectured extensively for the Society of Manufacturing Engineers, Society of Plastics Engineers, American Electroplaters and Surface Finishers Association and the Mass Finishing Job Shops Association. Mr. Davidson’s specialty is finishing process and finishing product development.
More about Dave Davidson…
I am a deburring and surface finishing specialist, consultant and advisor to SME’s [Society of Manufacturing Engineers] Technical Community Network. The focus of my activity is assisting manufacturers and machine shops with reducing their dependence on hand or manual deburring and finishing methods, and helping them to upgrade the edge and surface finish quality of their parts. I currently work from Colville, WA but I assist clients nation-wide. I can arrange for free sample processing and process development for your challenging deburring and finishing needs and can provide you with either contract finishing services or the in-house capability to produce improved hands-free finishes on precision parts. I can be contacted at 509.230.6821 or dryfinish@gmail.com. Let me know if I can be helpful.